Baratron Etch Manometer reduces zero drift
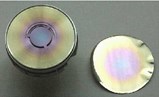
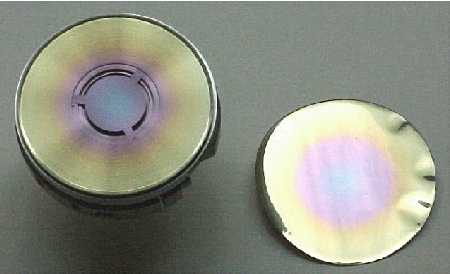
The new manometer design minimizes drift by significantly reducing deposits on the diaphragm. A channel machined into the lower vacuum housing of the manometer acts as a baffle between the vacuum chamber and the capacitance manometer diaphragm. The aspect ratio of the radial gas flow path is greater than 40:1. Molecules entering the sensor collide with boundary surfaces thousands (theoretically ~402) of times before reaching the diaphragm, increasing the likelihood that they will deposit on the channel walls. The channel protects the diaphragm from deposits while allowing the gas molecules to reach the diaphragm for accurate pressure measurement.
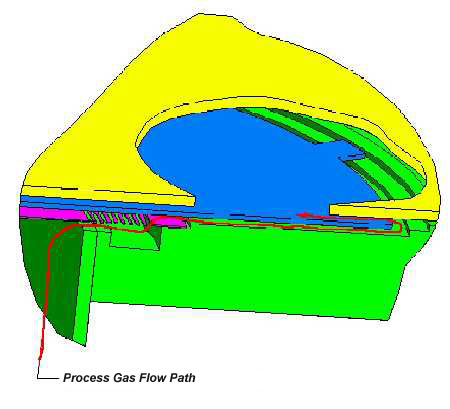
Particle contamination is another cause of process-related zero drift. In aluminum etch systems, for example, the aluminum chloride etch by-products can react with residual water or air to form particles of aluminum oxychloride and aluminum hydroxide. MKS Instruments' patented particle trap uses a two-stage approach to prevent particles from contaminating the diaphragm without affecting vacuum conductance or reducing response time.
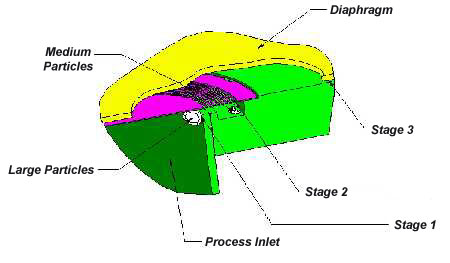
Particulate contamination is not exclusive to etch processes. All new Baratron 600B Series capacitance manometers now include this feature.
Results – Case study
Beta testing of the new Baratron Etch Manometer was conducted at Vitesse Semiconductor (Colorado Springs, CO). Prior to the installation of the Baratron Etch Manometer, Vitesse had significant problems with drift while performing an aluminum etch process with a TCP Lam 9600 metal etch system.
Mike Bouvy, a Vitesse equipment engineer, made the following observations in February of 1999: "As we run product, we see the drift occur … if the chamber sits idle, there is no drift. For a continuous 24-hour period of running product, we see a drift of about 1 mTorr/day. Typically, for every two days of running product, we have to re-calibrate the manometers."
Baratron Etch Manometer beta units were installed on March 30,1999. Six days later, this is what Mike Bouvy had to say: "I checked the logs, and there is no indication that the base pressures had drifted up on the daily checks over the weekend and no indication of being auto-zeroed. This has never happened before, and things are looking great with both styles of these manometers! Might be time for champagne!"
On Nov. 2, 1999, after six months with the new etch manometers, Bouvy said: "The new manometers have proven to be very reliable with virtually no drift over six months."
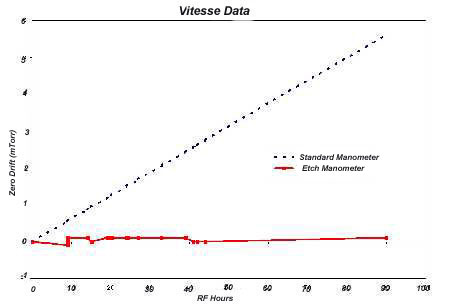
A simple cost/benefit analysis based on taking 10 minutes to re-zero every 24 hours, with downtime cost of $10K to $100K per hour, shows that eliminating downtime for re-zeroing translates to savings of $30K to $300K per month. In addition, the pressure measurements are more reliable.
Because of the small volume between the baffle and diaphragm, the time constant for gas to flow within the sensor is less than 10 milliseconds. The partial pressure of process by-product species is typically less than 10-7 Torr during the time that they are deposited. Their contribution to the total pressure being measured is insignificant, and trapping these molecules will not affect the pressure reading.
Source: MKS Instruments
Edited by Katherine Derbyshire
Managing Editor, Semiconductor Online
Baratron is a registered trademark and Etch Manometer is a trademark of MKS Instruments, Andover, MA, USA.